Enamel is basically a process of melting glass with a metal oxide-based color set onto the metal surface inside a specialized furnace at a high temperature of 700 to 900 degrees Celsius, and then cooling it down so that the enamel is fixed on the metal surface, this is a process that requires many repetitions until the product is perfect. The most common type of glass is a combination of silica, soda, lime, and a small amount of borac. There are many different ways to enamel dials, each of which requires unique skill and precision. The most common techniques in the world of high-end watches are Grand Feu, Cloisonné, Champlevé…
Cloisonné enamel is an ancient enameling technique, it was used to decorate metal objects with vitreous enamel, in even more ancient times it was also used to engrave precious stones, glass or other materials. This technique is formed by different areas of enamel, separated by bars of thin metal threads. Some of these threads are coated with thin gold by electroplating to prevent tarnishing during high-temperature enameling.
It can be said that MarkLE is the first rare unit in Vietnam to apply Cloisonné enamel on watch dials, a very complex technique that is done entirely manually by artisan hands during the preparation process until the product is finished. The entire manufacturing process is followed by an ancient technique by artisan MarkLE, ensuring that the finished product achieves a sophisticated finish, high aesthetics, and retains its color up to a hundred years.
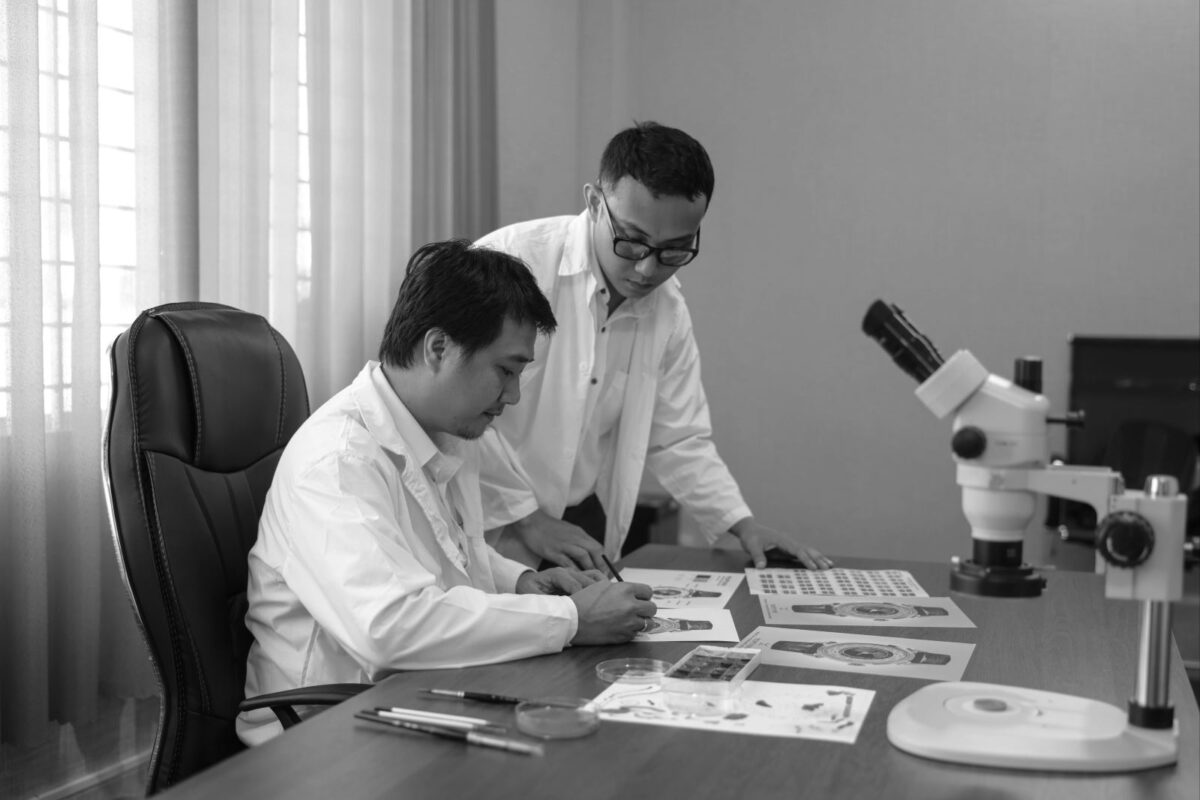
Color scheme for watch dials
Successful enameling is highly dependent on the preparation process. It start with choosing and using the right metal. The process of making Cloisonné enamel dials according to an ancient technique strictly followed by MarkLE goes through many steps: Making the dial work piece, bending the Cloisonné wire, gluing the Cloisonné wire to the dial workpiece, washing the glass enamel, painting the base glaze, rough sanding, painting the detail glaze and continue firing, fine sanding, polishing and finally microscopic examination of air bubbles in the enamel.
MarkLE has chosen gold, especially18k gold because of its compatibility with enamel, which destroys the oxide formation that affects the next enamel layer and is less deformed when fired at high temperatures. This is a material that has very little deformation when heated at high temperatures and does not change color due to oxidation at high temperatures.
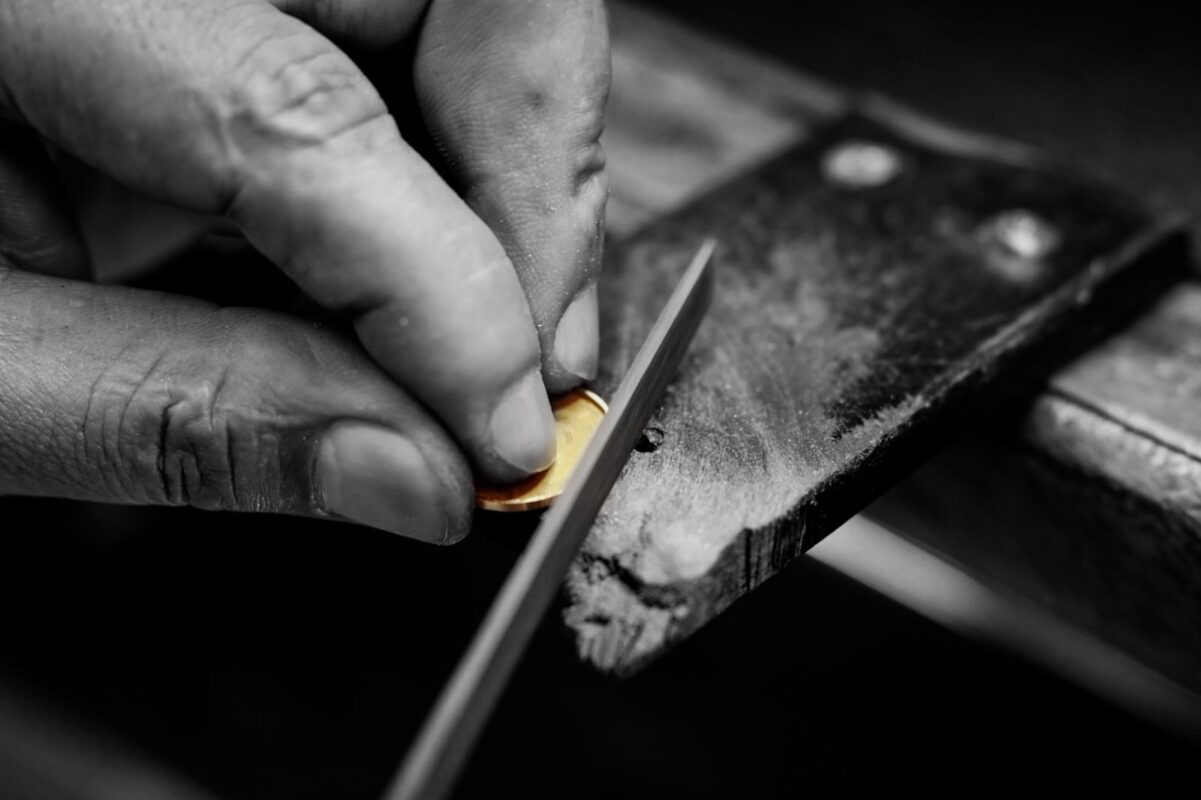
Handcrafted dial work piece
Along with the work piece of the dial, the Cloisonné threads are also made from gold with a thickness ranging from 0.03mm to 0.07mm depending on the requirements shown in each position on the enamel and they are arranged along the lines was sketched on the draft of the design so that the segments bend to right angles and the wire does not curl up.
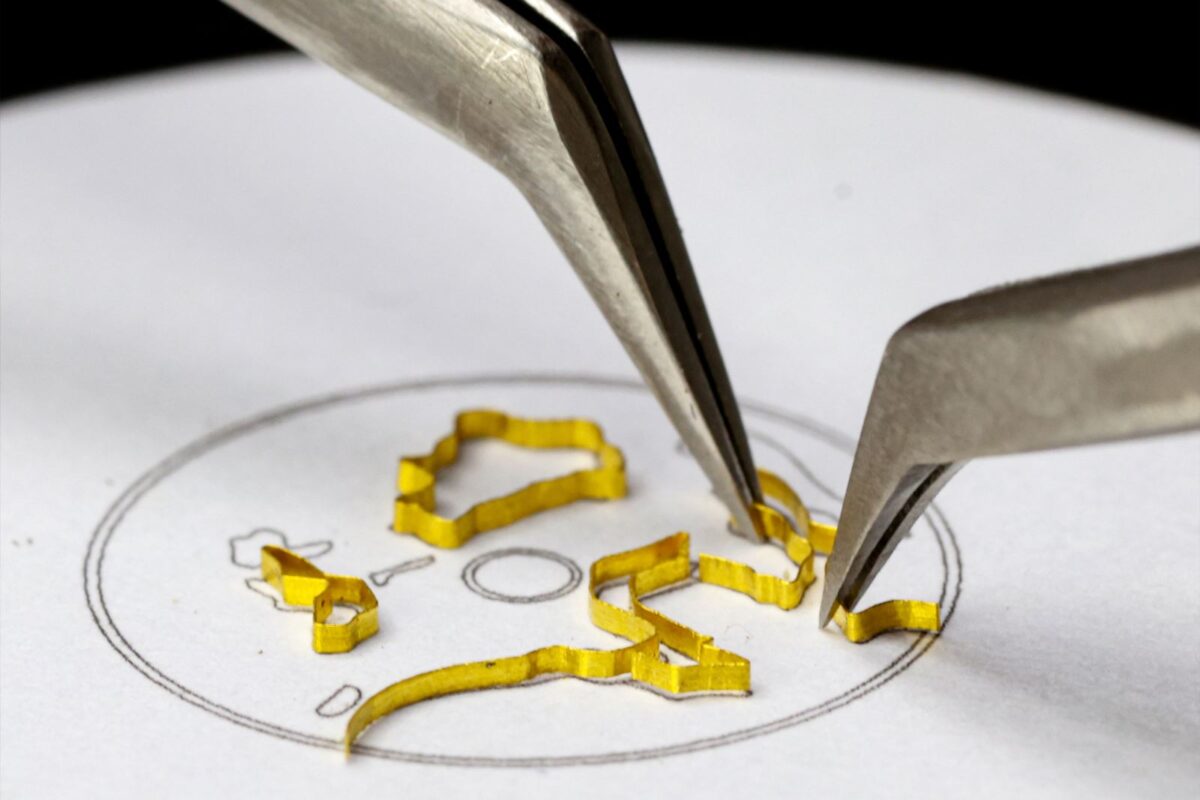
Cloisonné wire shaping
The process of wire forming as well as gluing is done with a small sharp pliers, two curved beak tweezers and a custom jig. All operations are performed under a stereo microscope with magnification up to 45X. This step requires the artist to have the most clever, skillful and aesthetic hands, because these threads will make the details sharper and create the most impressive depth for the beauty painting of the watch dial.
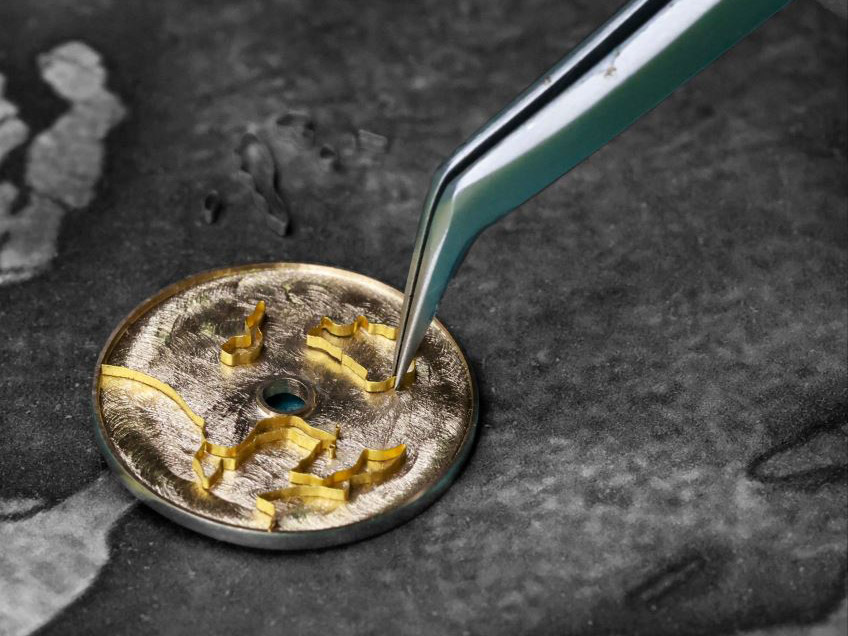
Stick the wire to the work piece according to the design
The sieving process of the vitreous enamel is very important, the enamel needs to be “washed” because too many fine particles in the transparent enamel can cause cloudiness. When washing the enamel, these very fine particles are removed. By grinding the enamel under the sizes of 80 mesh and 150 mesh sieves, the 80 mesh enamel is a mixture of particles ranging in diameter from 0.0070 inch to fine particles or dust size less than micrometer, it commonly used in screening techniques. After that, start washing the enamel with water and get a solution mixture. Continue repeating until the water in the enamel is not cloudy and transparent. After that, the enamel is stored in an airtight container, placed in a dry place and prepared for the enamel process.
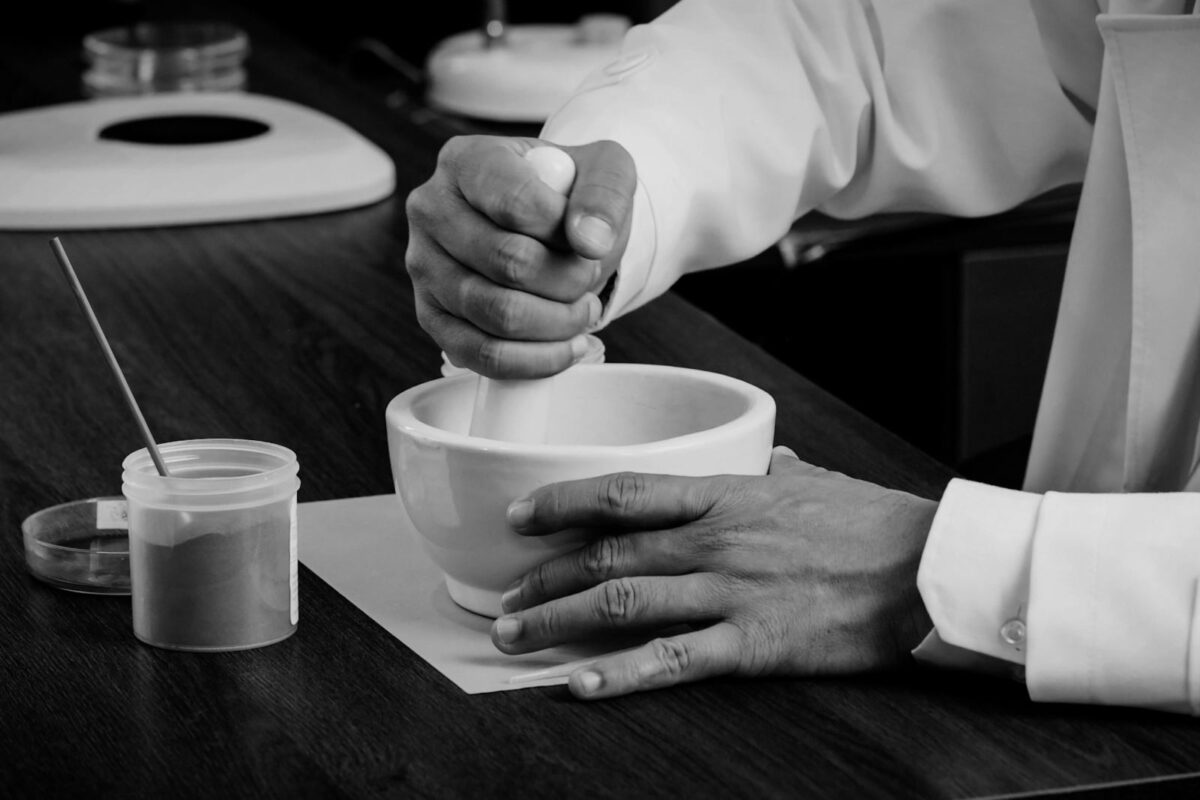
The process of grinding and washing enamel
The process of putting enamel on the work piece of watch dial is considered a prerequisite for the whole process because it requires total concentration, hand control to the smallest movements to be able to move the head brush to every detail, the smallest nook and cranny of the dial. The most difficult thing in this step is to put micro-enamel particles inside each of islands. The control of air bubbles in the enamel is also very important, even a small error can leave air bubbles in the enamel after firing. The most special thing is the process of choosing enamel color, MarkLE decided to use enamel color with dark blue to depict the sea, yellow, orange, and green transitions to represent the land. All create a harmonious overall color.
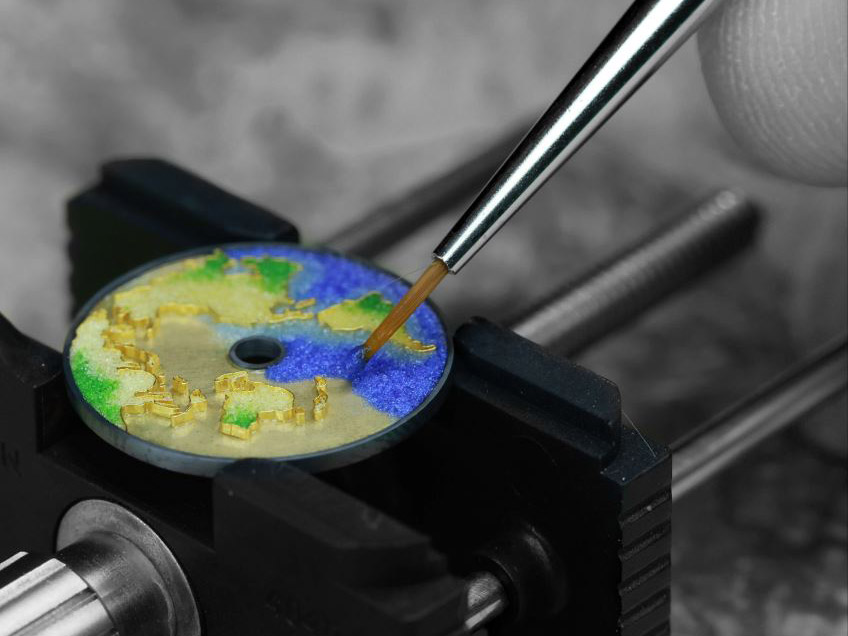
The process of painting enamel on the dial workpiece
The enamel firing process requires precise kiln temperature and firing time. MarkLE chooses a temperature from 700 to nearly 900 degrees Celsius for the process of firing opaque and transparent enamel. Each dial is enameled by MarkLE and fired between 12 and 15 times before rough sanding.
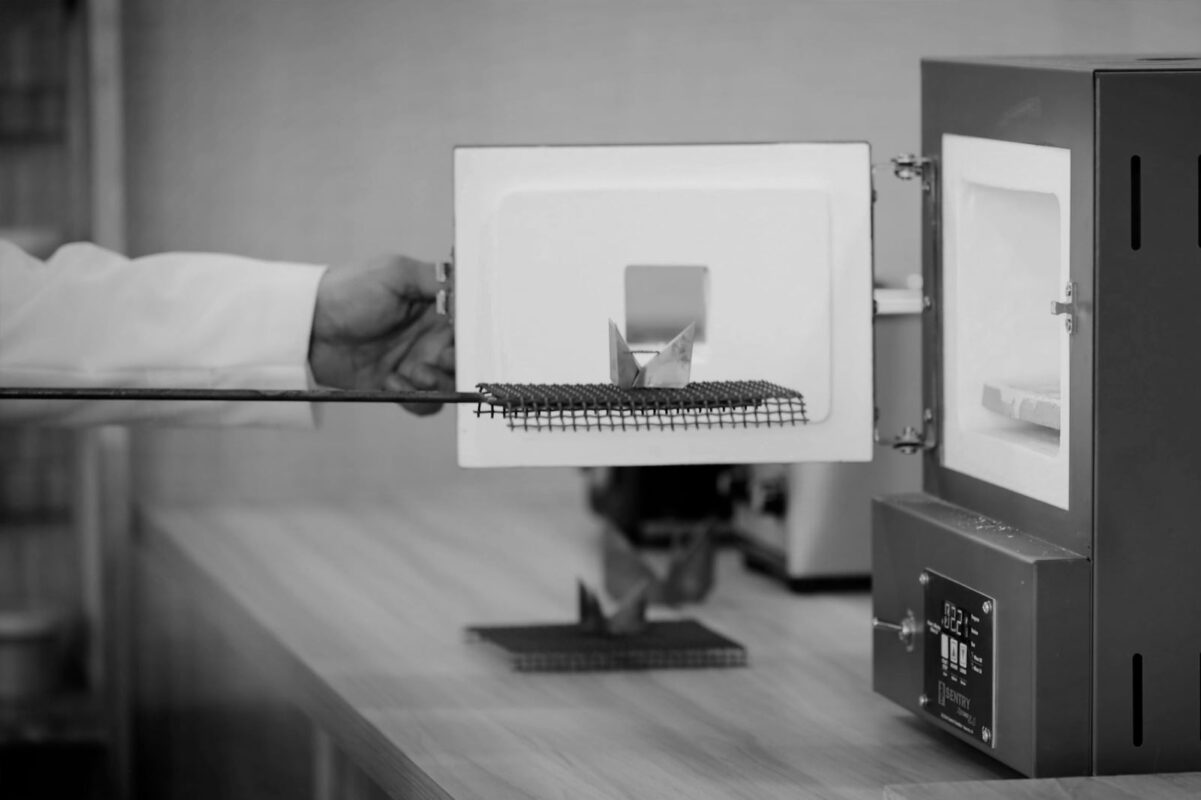
The process of firing enamel in a kiln
After finishing firing glaze many times, the dial is rough sanded to check for air bubbles on the enamel surface. The rough sanding step is done meticulously because this is a step that easily leads to enamel cracking, cracked dials after rough sanding will be removed, the rate of cracked dials at this step is over 80% of total finishing dial, the intact dials will be further enameled and fired.
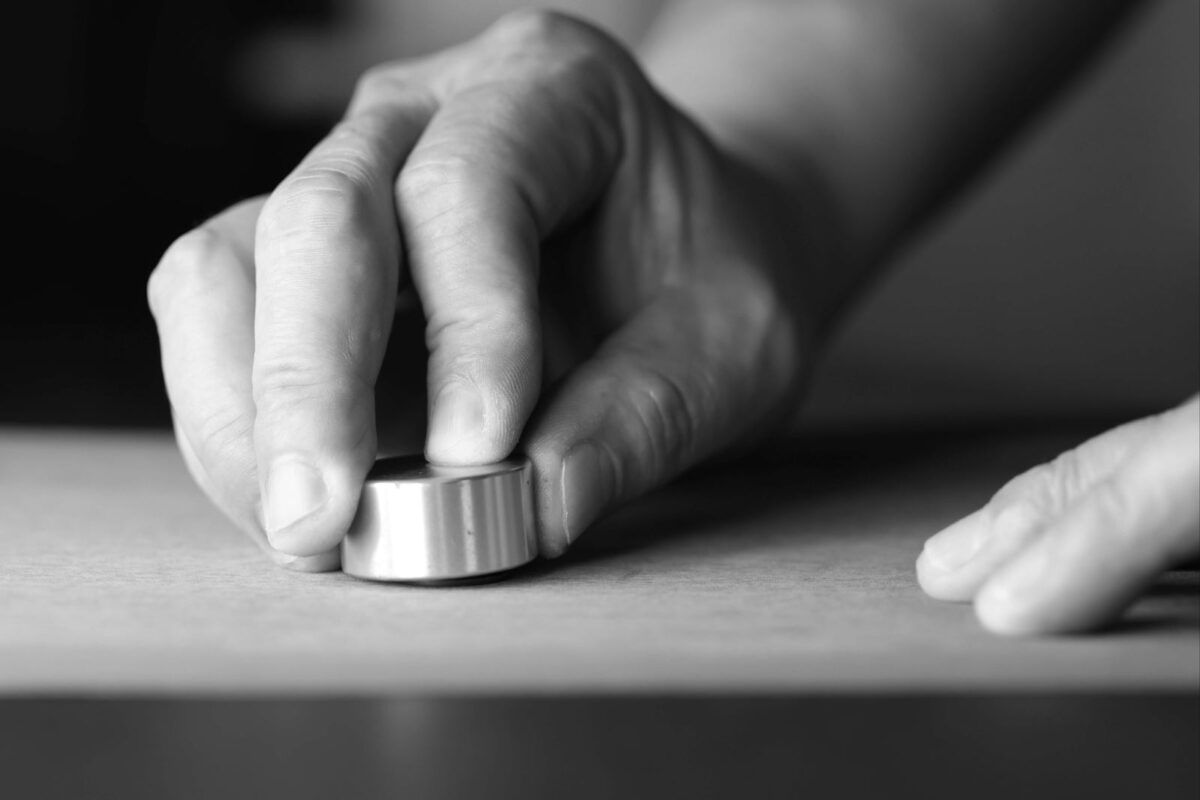
Rough sanding process
Rough sanding and checking for air bubbles in enamel are two very important steps, MarkLE will proceed to remove the dials with a lot of air bubbles, this selection process is very strict and is done under a microscop. The standard enamel surfaces at this stage will be further painted in detail and covered with protective enamel.
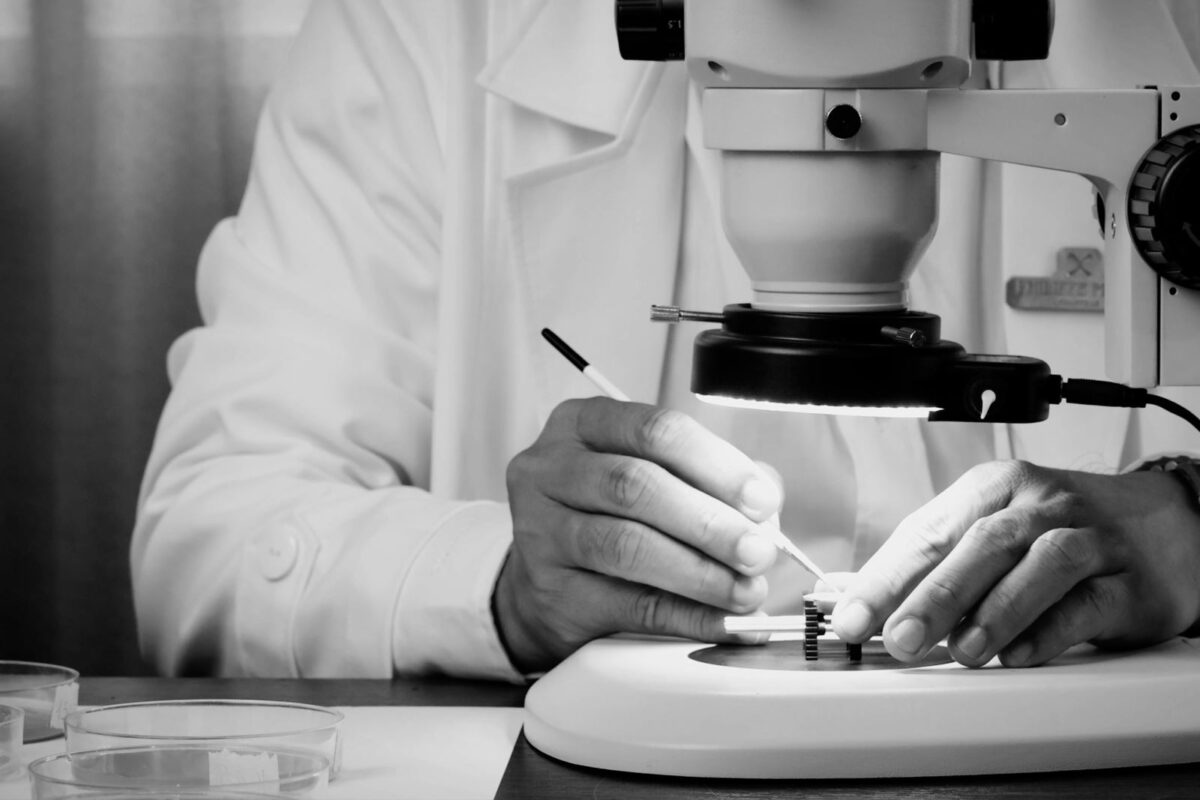
Detailed enamel painting for the dial
The process of enamel painting, firing, checking are repeated operations that take a lot of time. Selected enamel surfaces will be finely sanded to completely smooth the surface, creating depth and gloss for the product.
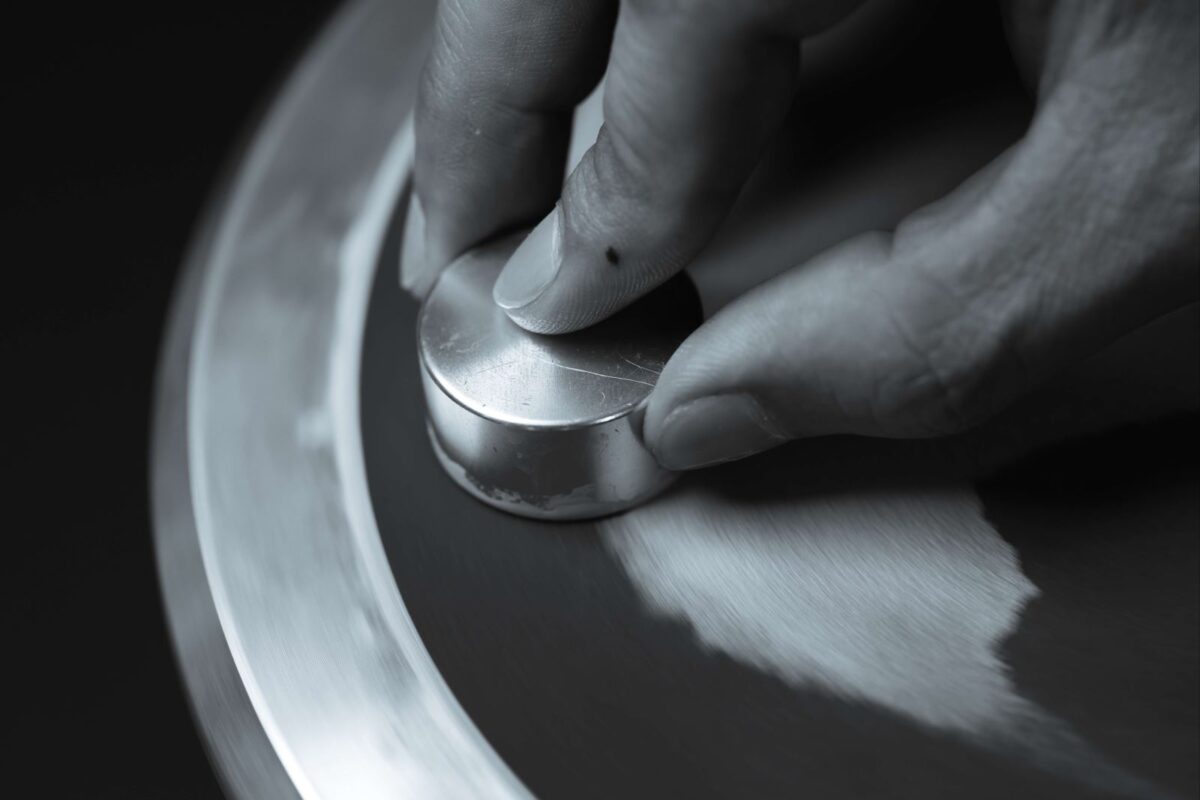
Fine sanding process
In order to bring users a perfect product, the product has to go through a process under the strict control of a dedicated team who has been relentless in creating quality works of art. Besides, time and temperature factors are considered top concerns. If the temperature is too low or the time is too short, the enamel will not adhere. If the temperature is too high or the firing time is too long, the enamel will become saturated with oxides from the metal, causing one or more changes such as burning at the edges, variation in color, changing in gloss, defects in appearance, and the fire control during the firing process are strictly controlled by MarkLE’s artisan.
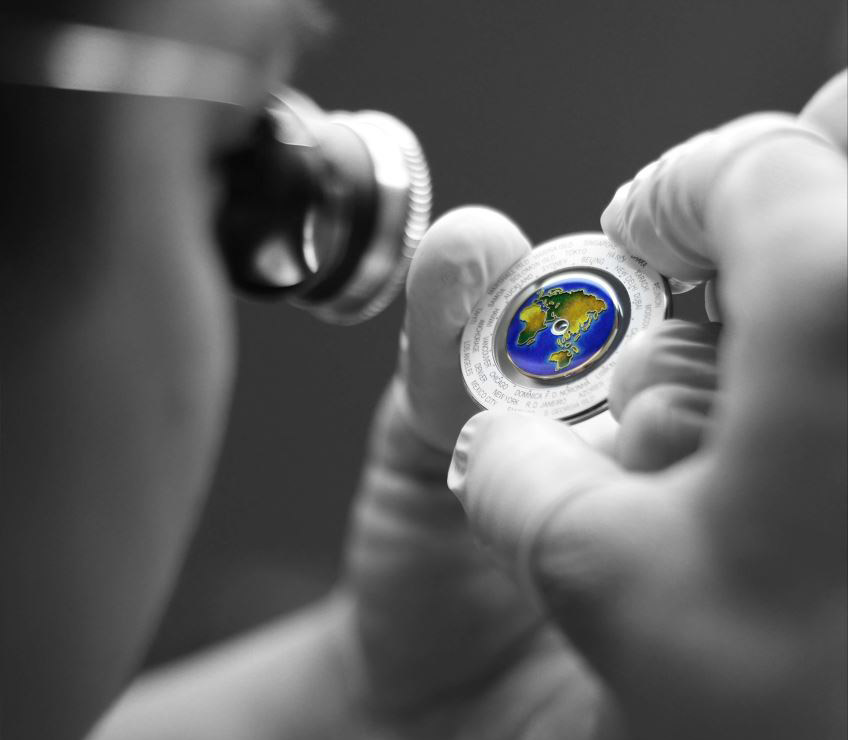
Final inspection step
With the complex and extremely sophisticated technique of Cloisonné enameling, it takes the artisans at MarkLE between 80 and 90 hours to craft a single Cloisonné enamel dial. However, one thing that is unavoidable is the appearance of tiny air bubbles on the enamel layer, leading to a significant reduction in product quality. But that cannot discourage MarkLE artisans and see it as a challenge to overcome. MarkLE has meticulously moved the needle tips to each small hole in order to break up the air holes and bring out smooth and harmonious textures on the dial surface. At MarkLE, the enamel face will be finely finished with almost no air bubbles or very few bubbles appearing in the enamel.
Cloisonné enameling is a complex task that takes a lot of time to craft with a very high failure rate in the finishing process. MarkLE understands that more learning is needed in the future to create Cloisonné enamels. That’s because nowadays, Cloisonné enameled watches are increasingly sought-after by the art world because those masterpieces remain valuable with time.